ACCT2102 Lecture Notes - Lecture 7: Weighted Arithmetic Mean
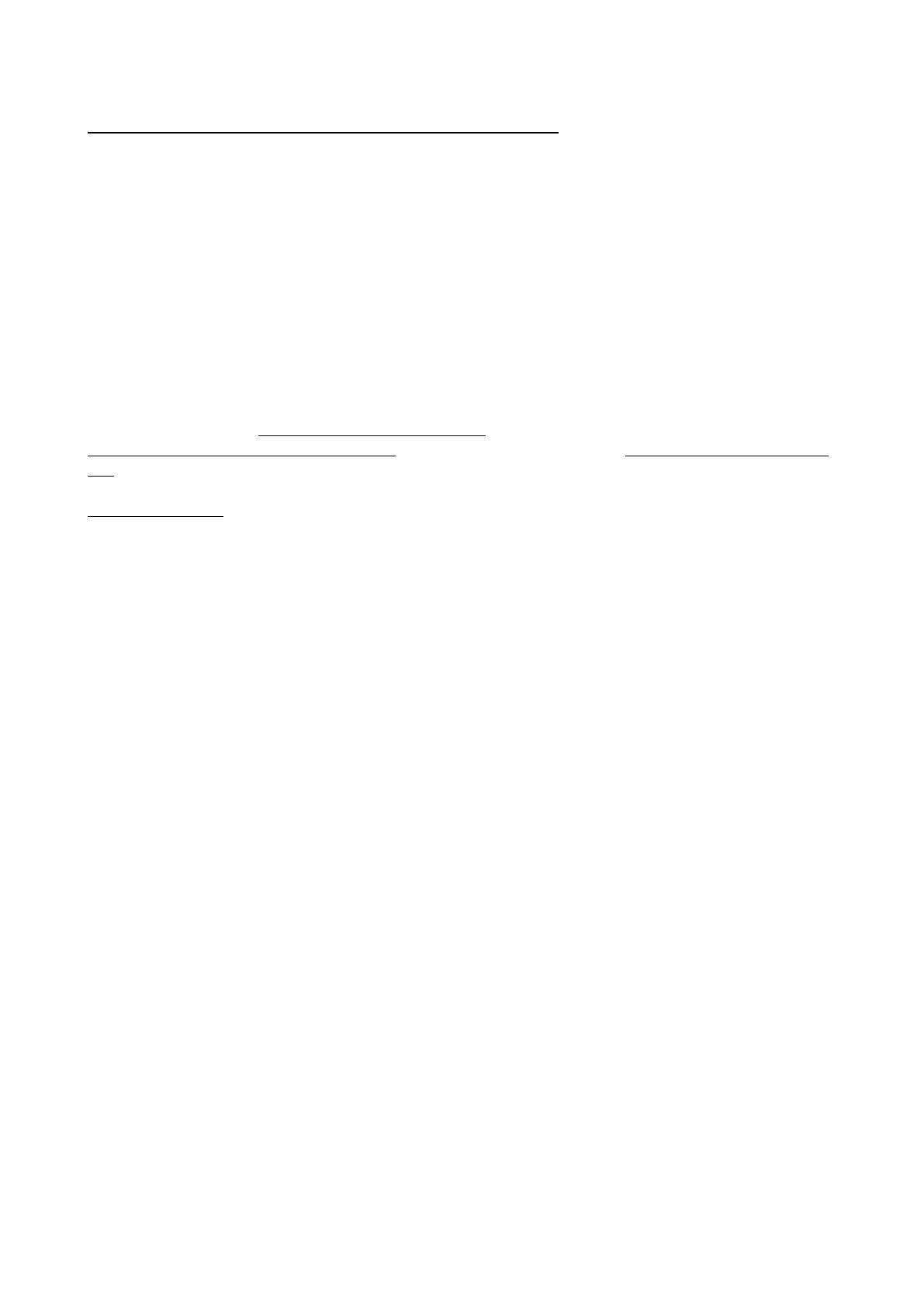
ACCT2102: Lecture 7 Spoilage, Rework, Scrap
Spoilage - units of production that do not meet the standards required by customers for good units and that
are discarded or sold at reduced prices.
Rework - units of production that do not meet the specifications required by customers but which are
subsequently repaired and sold as good finished units.
Scrap - residual material that results from manufacturing a product. It has low total sales value compared to
the total sales value of the product.
A company is justified in inventorying scrap when its estimated net realizable value is significant and the
time between storing it and selling or reusing it is quite long.
Normal spoilage: Spoilage inherent in a particular production process that arises even under efficient
operating conditions. Spoilage may be considered a normal characteristic of a given production cycle. The
costs of normal spoilage caused by a random malfunction of a machine would be charged as a part of the
manufacturing overhead allocated to all jobs. Normal spoilage attributable to a specific job is charged to that
job.
Abnormal spoilage:
abnormal spoilage is nonrecurring and avoidable.
Companies tend to aim to reduce spoilage as much as possible.
Reduce spoilage to almost zero (through higher-quality products, more customer satisfaction, more employee
satisfaction, and various beneficial effects on non-manufacturing (for example, purchasing) costs of direct
materials.)—> earn many potential savings of spoilage costs
Rework costs may include:
a. the labor and other conversion costs spent on substituting the new product
b. the costs of any extra negotiations to obtain the replacement product;
c. any higher price the existing supplier may have charged to do a rush order for the replacement product
d. ordering costs for the replacement product.
Scrap
-no distinction between normal & abnormal scrap
-Can account for specific job (direct) or common to all jobs (indirect)
-Recognised either at the time of its sale or at time of its production
-If scrap is immaterial, ignore. Record as scrap revenue.
-If scrap is material: its sales value is assigned to inventory (materials acc) and either:
-A) reduces the cost of a specific job (if direct)
-B) OH Control (if indirect)
1. Understand why businesses need to be aware of output that does not meet expectations
2. Distinguish among spoilage, reworked units, and scrap
3. Describe the general accounting procedures for normal and abnormal spoilage !
4. Account for spoilage in job costing and process costing (wtd avg only) !
5. Account for reworked units in job costing
6. Account for scrap in job costing !
1. Understand why businesses need to be aware of output that does not meet expectations
When they are aware of output not meeting expectations, they can control it and reduce
manufacturing defects which will reduce total costs. !
2. Distinguish among spoilage, reworked units, and scrap
There are 3 types of costs that arise as a result of defects: !
find more resources at oneclass.com
find more resources at oneclass.com