BU491 Lecture Notes - Lecture 9: Rooftop Photovoltaic Power Station, Crystalline Silicon, Canadian Solar
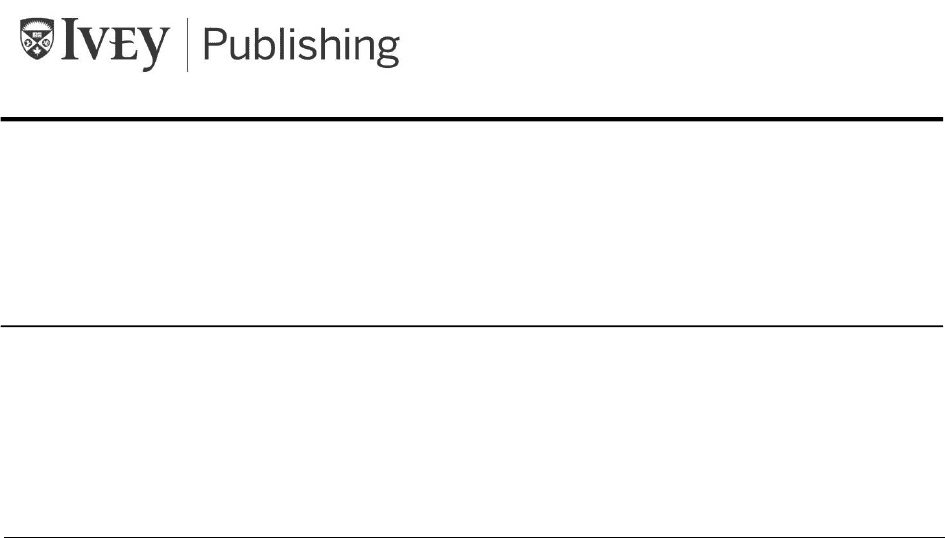
9B10M019
CANADIAN SOLAR
Jordan Mitchell wrote this case under the supervision of Professor Paul W. Beamish solely to provide material for class discussion.
The authors do not intend to illustrate either effective or ineffective handling of a managerial situation. The authors may have disguised
certain names and other identifying information to protect confidentiality.
This publication may not be transmitted, photocopied, digitized or otherwise reproduced in any form or by any means without the
permission of the copyright holder. Reproduction of this material is not covered under authorization by any reproduction rights
organization. To order copies or request permission to reproduce materials, contact Ivey Publishing, Ivey Business School, Western
University, London, Ontario, Canada, N6G 0N1; (t) 519.661.3208; (e) cases@ivey.ca; www.iveycases.com.
Copyright © 2010, Richard Ivey School of Business Foundation Version: 2014-11-19
In late September 2009, Dr. Shawn Qu, CEO, president, chairman and founder of Canadian Solar, was
constantly on the move. His company, a NASDAQ-traded solar cell and module manufacturer, had grown
at a compound annual growth rate (CAGR) of 135.7 per cent over the last five years from $9.7 million in
revenues in 2004 to $705 million in 2008 (see Exhibit 1 for key financials). The strong growth had been
spurred by an increasing number of government incentive programs to encourage the adoption of solar
photovoltaic (PV)1 technology. For the past couple of years, solar energy was seen to be the world’s fastest-
growing industry. However, the credit crunch and global economic downturn combined with changes to
Spain’s incentive program had put the worldwide PV industry into oversupply for the first half of 2009.
During the summer, demand changed again. Forecasts were exceeded, causing a temporary undersupply of
ready-to-install solar modules. The fluctuating solar demand had caused analysts to change their financial
outlook for Canadian Solar several times throughout 2009. In mid-2009, a Deutsche Bank analyst had
predicted full-year sales to come in at $395 million with net losses at -$18 million, only to revise the outlook
two months later to sales of $574 million and net income of $49 million.
Part of the increasing positive outlook was attributed to government incentive programs. Of particular
interest to many players, including Canadian Solar, were proposed incentive programs in China and Canada.
In Ontario, for example, the details of the provincial government’s incentive program for green energy —
the Feed-in Tariff (FIT) program — had just been released with specific requirements for domestic content.
Although registered as a Canadian company, Canadian Solar had the bulk of its production operations in
China; namely, seven facilities dedicated to the manufacture of different solar PV components. And, even
though the company’s “bases” were in China and Canada, 89.5 per cent of 2008 revenues came from
Europe. Company management expected that to change rapidly as they were planning or had already
established new sales offices in South Korea, Japan, China, Italy, Spain, Germany, the United States and
Canada.
When looking at the relatively nascent and rapidly growing solar PV industry replete with a mix of diverse
competitors, Qu and other Canadian Solar senior managers wondered how best to compete in the
increasingly “global” PV industry.

Page 2 9B10M019
SOLAR ENERGY
Solar energy was divided into three main categories: solar electric, solar thermal and concentrating solar.
Solar electric converted the sun’s energy into electricity and solar thermal used the sun for heating or
cooling. Concentrating solar power mixed solar electric and solar thermal as it used small optical mirrors
to collect solar energy and convert the sunlight to heat. The heat was then applied to a liquid or gas to turn
a turbine, thereby creating electricity.
The other important distinction in solar energy was between “grid-tied” and “off-grid” applications. Gridtied
applications were solar-electric systems that were connected to an electricity utility grid (in nearly all
jurisdictions, electricity utility grids were heavily regulated by government bodies and were often separate
from electricity providers). Grid-tied applications were either “ground mount” or “rooftop” — ground
mount applications were typically in a field or desert area and were either solar PV or concentrating solar
power. Grid-tied rooftop projects ranged from one kilowatt to 10 kilowatts (kW) on residential homes to
larger projects of 10 kilowatts to five megawatts (MW) on commercial buildings.
Off-grid applications were defined as a system completely independent of the main electricity grid. Offgrid
applications ranged from tiny solar cells in pocket calculators to solar-thermal systems for hot water tanks
in residential homes. In the last few years, off-grid applications had become popular for road lights, signs
and parking meters whereby a solar module was placed on top of the apparatus to provide power at night
through a battery. Off-grid applications were also seen as one solution to providing power in isolated rural
areas.
PHOTOVOLTAIC CELLS2
The main tenet of solar-electric power was the photovoltaic (PV) cell, which used the “photovoltaic effect”
to generate electricity. When sunlight hit a PV cell, electrons bounced from negative to positive, thus
producing electricity. In order to generate electricity, a PV cell required a semiconductor material and
positive and negative poles.3
The most common semiconductor material for PV cells was silicon.4 For most solar applications, the silicon
was refined to 99.9999 per cent purity, which was known as 6N silicon (the number “6” referred to the
number of “9s”). Companies such as Canadian Solar had commercialized products with lower grades of
silicon for solar applications. For example, upgraded metallurgical-grade silicon (UMG-Si) was one such
type of lower grade silicon. It was 99.999 per cent pure (or 5N for five “9s”). UMG-Si was a biproduct of
the aluminum smelting business and historically had been less expensive than 6N silicon.
The three types of PV cells were polycrystalline (“poly”), monocrystalline (“mono”) and amorphous (“thin-
film”). Poly PV cells used silicon in its refined state whereas mono took the refinement a step further, thus
creating higher efficiency (the drawback with mono PV was the higher cost of production vs. poly). The
third type, thin-film, was substantially different in that it did not have crystalline silicon, but rather a painted
or printed semi-conductor. There were six main types of materials used in thin-film, although three had not
yet been proven to be commercially viable.5
The basic process of constructing a crystalline PV cell began by forming cylindrical ingots from the
semiconductor material. The ingots were then cut into very thin disc-shaped wafers. The wafer was etched
with hydrofluoric acid and washed with water, creating a PV cell. To create a usable “solar module” (also
called a “solar panel”), a series of PV cells were placed in between a sheet of glass held in by an aluminum
frame and plastic backing connected to a cable plug. In most installations, a number of modules were used
to make up an array. The array was then connected to an inverter (to convert the electricity from direct
current (DC) to alternating current (AC)).

Page 3 9B10M019
Solar modules were rated by their capacity in watts (W). Most solar PV modules were rated between 80W
and 250W. Larger solar modules (200W+) weighed approximately 20 kilograms and were sized 1.6 meters
long, one meter wide and four to five centimeters thick. Solar efficiency — the amount of sunlight energy
converted to electricity — ranged between 12 and 18 per cent for most PV modules. However,
breakthroughs were constantly being achieved — as of mid-2009, the highest PV cells had efficiency ratings
slightly above 23 per cent. As a general rule of thumb, one to two per cent efficiency was deducted from
the rating of the cell to determine the rating of the module (i.e. an 18 per cent efficient cell would have a
16-17 per cent efficient module).
The cost of PV cells was a constantly moving target. In securing contracts with large volumes, it was
common for PV manufacturers to offer discounts of 10 – 30 per cent on the price of a module. In largescale
projects, many buyers saw PV modules more as a commodity product and were largely concerned with the
price per watt. From 2007 to 2009, the selling price of a solar PV (from a PV module manufacturer to a
customer) had increased slightly from $3.50 per watt to around $4 before dropping to approximately $2.50
per watt (put another way, the price for one 200W solar PV crystalline module was about $500 as of mid-
2009).
A major driver behind the price of solar PV was the price of silicon. A temporary silicon shortage around
mid-2008 pushed the spot price of silicon to over $500 per kilogram (up from around $25 per kilogram in
2004). However, by mid-2009, that price had fallen to around $60 per kilogram.6 As the supply of silicon
increased along with greater manufacturing efficiencies, the cost for crystalline PV modules was expected
to fall below $1 per watt in two to three years.
Many industry insiders debated whether thin-film modules held more promise given their lower cost versus
poly and mono modules. As of August 2009, the price of thin-film was reported at $1.76 per watt versus
$2.50 per watt for silicon modules.7 Despite silicon’s current higher price, crystalline silicon supporters
often pointed to the fact that thin-film would have trouble competing as the price of crystalline modules
dropped. Additionally, poly and mono crystalline silicon modules typically enjoyed higher efficiencies than
thin-film and required less space, fewer mounting systems and less cabling for the same power output.
In addition to the cost of the module itself, the cost of installation ranged from $4 to $8 per watt. Developers
of utility-scale PV projects also had to be mindful of the real estate cost and electricity transmission costs.
All tallied, the cost of solar PV was between 0.15 and 0.35 per kilowatt-hour (kWh) versus non-renewable
sources of energy between 0.03 and 0.15 per kWh. As scale efficiencies grew along with technological
breakthroughs, many insiders felt that the cost of solar would be competitive with nonrenewable sources in
a three to five year time horizon (this was referred to in the industry as reaching “grid parity”).
THE GLOBAL SOLAR INDUSTRY
In 2008, solar PV experienced its largest increase to date by growing 5.6 gigawatts (60.8 per cent) to 14.73
gigawatts (GW) in 2008.8 (On a global level, solar power accounted for under one per cent of all electricity
generation.) Geographically, total installed capacity was split: 65 per cent in Europe, 15 per cent in Japan
and eight per cent in the United States. In 2008, the strongest market was Spain, which represented nearly
half of the installations due to its aggressive Renewable Energy Feed-in Tariff (referred to as REFIT or FIT)
program, which guaranteed electricity rates for certain renewable projects. Even though Spain dominated
the PV market in 2008, the Spanish government had placed a 500MW cap on annual installations for the
next two years, given uncontrollable growth. Thus, Spanish PV installations were expected to drop
substantially in 2009. Germany was the second largest market, capturing 26.7 per cent of worldwide
installations during the year (Germany was one of the first countries in the world to introduce a FIT
program). Other leading solar countries were the United States (six per cent of worldwide installations),
South Korea (five per cent), Italy (4.9 per cent) and Japan (four per cent).
Document Summary
Jordan mitchell wrote this case under the supervision of professor paul w. beamish solely to provide material for class discussion. The authors do not intend to illustrate either effective or ineffective handling of a managerial situation. The authors may have disguised certain names and other identifying information to protect confidentiality. This publication may not be transmitted, photocopied, digitized or otherwise reproduced in any form or by any means without the permission of the copyright holder. Reproduction of this material is not covered under authorization by any reproduction rights organization. To order copies or request permission to reproduce materials, contact ivey publishing, ivey business school, western. University, london, ontario, canada, n6g 0n1; (t) 519. 661. 3208; (e) cases@ivey. ca; www. iveycases. com. Copyright 2010, richard ivey school of business foundation. In late september 2009, dr. shawn qu, ceo, president, chairman and founder of canadian solar, was constantly on the move.