MGT 250 Lecture Notes - Lecture 60: Stockout, Finished Good
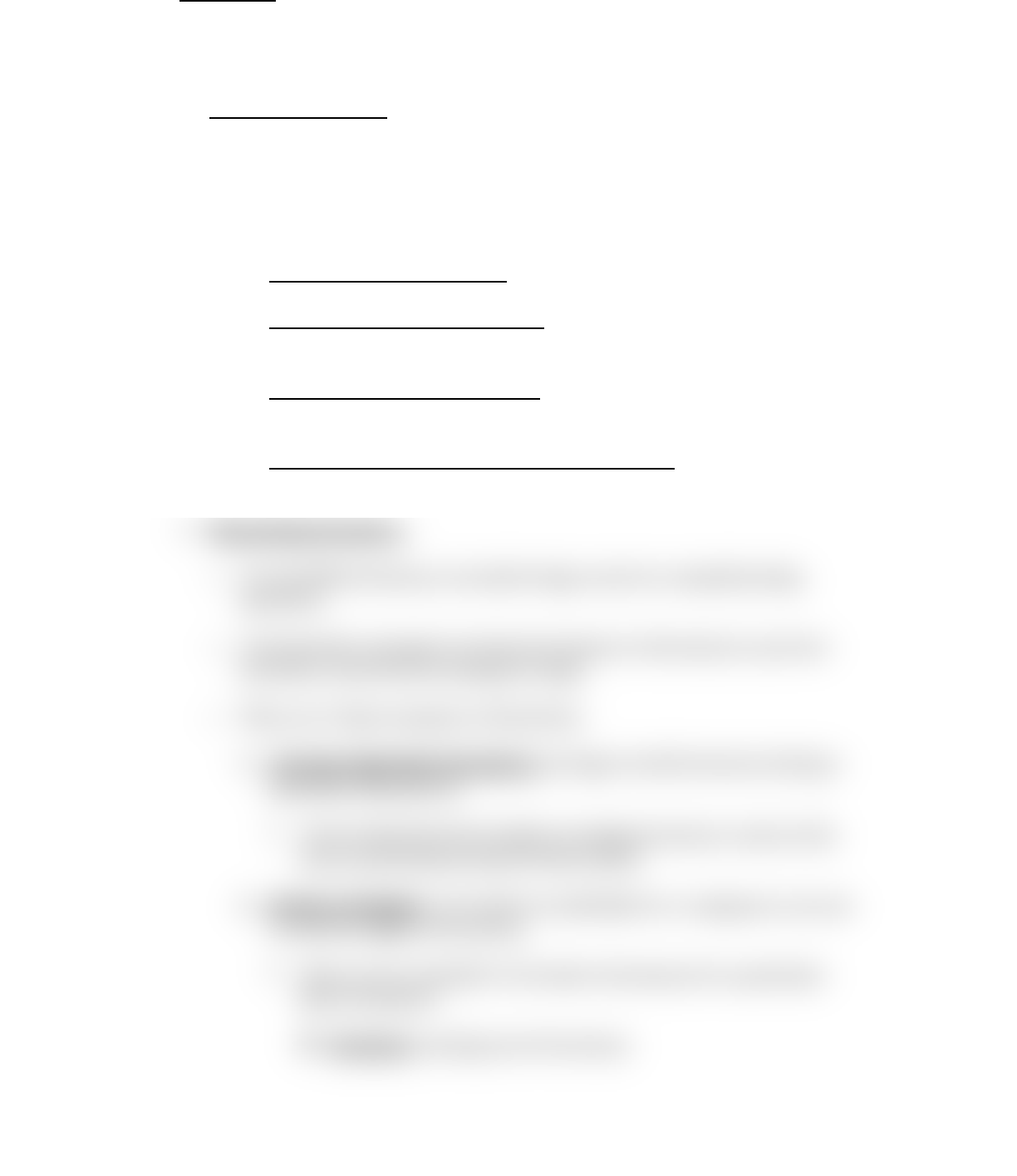
• Inventory:
➢ Amount & # of raw materials, parts, & finished products that a company has
in its possession.
➢ Types of Inventory:
o The flow of inventory through a manufacturing plant begins when
purchasing department buys raw materials from vendors.
o There are 4 kinds of inventory a manufacturer stores:
1. Raw Material Inventories: basic inputs in manufacturing process.
2. Component Parts Inventories: basic parts used in manufacturing a
product.
3. Work-In-Process Inventories: known as partially finished goods &
also called initial assembly.
4. Finished Goods Inventories/Final Assembly: final outputs of
manufacturing process.
➢ Measuring Inventory:
o Uncontrolled inventory can lead to huge costs for a manufacturing
operation.
o Consequently, managers need good measures of inventory to prevent
inventory costs from becoming too large.
o There are 3 basic measures of inventory:
1. Average Aggregate Inventory: average overall inventory during a
particular time period.
▪ Can be determined by simply averaging inventory counts at the
end of each business day for that month.
2. Weeks of Supply: # of weeks it would take for a company to run out
of current supply of inventory.
▪ There is an acceptable # of weeks of inventory for a particular
kind of business.
❖ Stockout: running out of inventory.
find more resources at oneclass.com
find more resources at oneclass.com